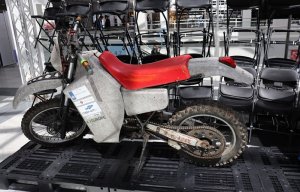
Bright prospects for reinforcements underlined at Techtextil 2019
With the Demonstrator Light Textiles, ITA shows an illuminated textile by using light-guiding fibres and polymer optical fibres (POF).
13th May 2019
Innovation in Textiles
|
Aachen
Ambient lighting – Demonstrator Light Textiles. © ITA
The Institut für Textiltechnik of RWTH Aachen University (ITA), will present its expertise in the field of ambient lighting at Techtextil 2019 on the Elmatex stand this week. The Institute will present a Demonstrator Light Textiles that shows a new type of energy storage system for furniture applications, a range of textile products and new materials for aerospace applications.
With the Demonstrator Light Textiles, ITA shows an illuminated textile by using light-guiding fibres and polymer optical fibres (POF). The polymer optical fibre (POF) demonstrator was developed as part of an ongoing cooperation between Mentor and the ITA. This is an R&D model that offers ITA's industrial partners the opportunity to conduct targeted research in a specific field and to train qualified employees.
It is suited to design illuminated surfaces in the interior, for example, in the automotive or home sector. This textile solution is designed to offer a flexible, drapable surface with a soft, pleasant feel in a limited space. ITA provides the fibre and process development.
The remote-controlled model vehicle with fuel cell drive (RC-Car) is an emission-free model car with lightweight tanks and body made of fibre composite plastics (FRP). It consists of kits from Tamiya-Carson Modellbau and Horizon Fuel Cell Technologies.
Remote-controlled model vehicle with fuel cell drive. © ITA
The pressure vessels (Composite Pressure Vessel-CPV) of the RC-Car were manufactured by ITA with a new winding technology for pressure vessels with carbon fibres on a machine from Murata, Japan. The CPVs are produced by multifilament winding, which promises a higher productivity than conventional wet winding. They CPV can withstand high pressures, for example, 700 bar, and are said to offer significant weight savings compared to batteries.
The CPVs are said to enable emission-free, long-range, hydrogen-based propulsion that can be refuelled quickly and represents ITA's contribution to mobility and energy revolution. “The CPVs contribute to a sustainable energy balance, since, for example, rare earths are not required as in battery production,” the company reports.
“The target group for the CPVs is the transport sector. In the automotive industry, CPVs provide the basis for a lighter drive concept, as they can be charged more quickly and offer greater lightweight potential than batteries. For the aerospace sector, the new winding technology represents an alternative, faster manufacturing process to wet-willing pressure vessels.”
With its new sports bra, ITA shows a newly developed innovative process for the highly productive manufacturing of 3D knitted fabrics on large circular knitting machines without additional separating and joining steps. “Large circular knitting is significantly faster and more efficient than flat knitting which was previously used,” the Institute reports.
Sports bra. © ITA
The garments can be tailored seamlessly and individually to size in a single step and are thus an example of a store-factory approach, i.e. customer-specific just-in-time production in a specialist shop on site. “This new process is patented and forms the basis for licensing this technology to new business fields and other industries,” the Institute adds.
Many nations are toying with the idea of setting up a lunar station and to use the moon as a source of raw materials, a research site, a stepping stone into the solar system and a tourist destination. But the transport of the material for a lunar station is very costly: to bring material from the earth to the moon costs up to EUR 1 million per kilogram. For a lunar station, at least 450 tons are needed.
MoonFibre – from regolith to textiles. © ITA
“ITA’s solution is to produce directly on the moon,” the Institute explains. “A lot of moon rock is very similar to basalt. ITA has already developed a production process to spin mineral fibres based on lunar rock.”
Within MoonFibre, ITA uses this experience for the production of fibres for the reinforcement of 3D structures on the basis of moon rock and produces the fibres for the construction of the moon station directly on site. ITA’s approach is supported by the German Aerospace Center (DLR). In addition, the project is funded by crowd funding.
Business intelligence for the fibre, textiles and apparel industries: technologies, innovations, markets, investments, trade policy, sourcing, strategy...
Find out more