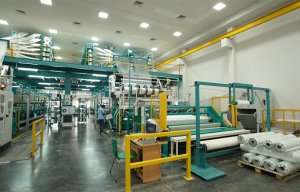
SKAPS acquires Matrix Composites
Today, experts in tissue engineering are near to perfecting the replication of a different and much more benign kind of matrix than that of 1999.
10th November 2016
Innovation in Textiles
|
Geneva
In the dystopian future of the famous 1999 film starring Keanu Reeves, our existence – as it is perceived by most human beings – is actually a simulated reality called ‘The Matrix’. It has been deliberately created by sentient machines to subdue the human population, while the heat and electrical activity from their bodies is farmed for energy.
Today, experts in tissue engineering are near to perfecting the replication of a different and much more benign kind of matrix – but one that back in 1999 was just as much the stuff of science fiction.
It’s the fibrous, artificial extracellular matrix (ECM) that is to be found in the tissues of human skin, bones and tendons – and engineered nanofibre nonwovens are proving crucial to its development.
ECMs consist of interwoven protein fibres with diameters in the range from tens to hundreds of nanometres.
Collagen, for example, forms fibre bundles with diameters of 50-500nm and is the main component of natural ECMs for many tissues, including skin, bone, and tendons. The nanofibrous structure of ECMs offers a network to support cells and to present an instructive background to guide cell behaviour.
The development of scaffolds that possess similar morphological structures to natural ECMs, however, remains a major challenge in tissue engineering.
Currently, there are three methods for preparing nanofibre scaffolds, explain scientists from South Dakota Board of Regents in world patent WO/2016/105581 – self-assembly, phase separation and electrospinning, but all have limitations.
Employing the self-assembly method, it is difficult to control the pore size and shape inside a scaffold and most self-assembled scaffolds are prepared in a liquid environment, resulting in relatively weak mechanical properties.
With the phase separation method there is little control over the fibre diameter and orientation in a scaffold and the preparation time can be long. In addition, the method can only generate small pores with sizes up to about 10 μm. Although the phase separation method can be combined with a technique called “porogen leaching” to make the required macropores with sizes from tens to hundreds of micrometres, such an approach is usually time-consuming and the complete removal of the porogen from the resulting scaffold is often difficult.
The electrospinning method can be applied to a wide range of materials. The small diameters and the large surface area of electrospun nanofibres, as well as the porous structures of electrospun nanofibre webs, can facilitate cell adhesion, proliferation, migration and differentiation. These advantages make them well-suited for tissue engineering.
Their major limitation, however, is the morphological structure of overlaid nanofibre mats, with pore sizes in sub-micrometres which lack the required macropores for cell growth.
The South Dakota scientists have consequently developed a method for fabricating electrospun 3D nanofibre scaffolds with interconnected and hierarchically structured pores and high porosities. These better mimic natural ECMs and maximise the likelihood of long-term cell survival and the resulting generation of functional tissue in a biomimetic environment.
Addressing similar objectives, Xanofi, based in Raleigh, North Carolina, has adopted the wet-laid nonwovens process for the production of 3D cell culture supports.
In its recent patent WO/2016/080954, Xanofi explains that cells cultured on flat 2D cell culture surfaces do not necessarily represent an in vivo like atmosphere and often result in artificial 2D sheets of cells. 3D cell culture is a growing field and there have been numerous products developed to provide in vivo-like organisation and scale. Approximately 30% of cell culture scientists are already estimated to have switched from 2D to 3D cell culture.
Products developed to address the needs of the growing 3D cell culture market, the company explains, include hydrogels, sol gels, ceramic scaffolds, expanded polystyrene supports and permeable membranes, as well as electrospun nanofibre layers.
However, although providing either a multi-layer or etched surface for cell growth, these products fail to truly mimic the chaotic, 3D fibrous structure of the ECM deposited by cells growing in living tissue.
Xanofi has developed a method for creating 3D cell culture supports using short-length nanofibre slurries and nanofibre/ microfibre mixed composite substrates
The staple polymeric nanofibres can be either wet-laid onto a fabric substrate, wet-laid with other fibres to form the nonwoven substrate, or wetlaid as dried nanofibres only. The dried substrates are then cut into discs and placed into individual culture wells, or can be cut to any size from the flat sheets.
Culture media and living cells can then be added to the discs to give the cells a rigid substrate that contains randomly oriented nanofibres throughout the entire thickness of the substrate. The nanofibres mixed with microfibres can also be put into slurry form in cell culture medium and provide a structure that can be invaded and remodelled as part of the cell’s normal tissue growth.
In 2014, Xanofi introduced XanoMatrix as its next generation 3D cell scaffold substrate. Incorporating staple nanofibres throughout the Z-axis of a substrate, cells have the ability to migrate and reshape the scaffold in new ways – the closest ECM mimic on the market today, the company says.
A wide range of nonwovens for healthcare applications will be showcased at the INDEX™17 exhibition – from engineered materials for wound care or infection prevention to specialised fabrics for blood filtration and implants. In other medical products, especially for filtration applications, nonwovens are employed as the supporting layers for nanofibre webs and also in finely-tuned combinations of differing fibre structures.
At INDEX™17, taking place from 4-7 April 2017 at Palexpo in Geneva, four dynamic nonwovens industry applications will be highlighted. Accompanied by high-level keynote speakers, free conferences and tutorials, the Transportation, Medical, Geotextiles and Filtration segments have been singled out for special focus.
In addition, for the first time, the well-renowned FILTREX conference will take place in parallel with INDEX™, on 5 and 6 April.
Register to receive latest news and developments from INDEX™17
Business intelligence for the fibre, textiles and apparel industries: technologies, innovations, markets, investments, trade policy, sourcing, strategy...
Find out more