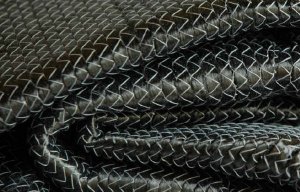
Zoltek PX35 expansion in Mexico
New developments in flywheel technology have driven energy storage costs to be very competitive with other energy storage methods, says Bill Regan.
30th September 2014
Innovation in Textiles
|
Cologne
Bill Regan will be presenting a topic entitled Energy storage flywheel applications - how significant an opportunity is this for carbon fibre? on 9 October, the first day of the conference, as part of the session dedicated to planes, turbines and automobiles applications for high performance carbon fibre.
Bill Regan has over 30 years of experience in the composite industry designing and building composite structures in marine and industrial applications.
Most recently his involvement in the composite industry has been directing advances in carbon fibre manufacturing operational efficiencies as Vice President of Engineering & Technology for Zoltek and directing new developments in intermediate carbon fibre products as General Manager of Entec Composite Machines.
There is a very large opportunity for flywheel energy storage systems in residential homes due to their compact size and very high efficiency, Bill Regan believes.
“In transportation, KERS or kinetic energy recovery systems that use the moving vehicles braking system to recover kinetic energy have been used in race cars and now are starting to be developed for passenger vehicles. Industrial applications for storage systems in plants for off peak energy production offer significant opportunities for flywheels,” he said.
“The potential cumulative flywheel market over the next 15 years could be well over $65 billion in sales. The global flywheel energy storage market is currently forecasted to grow at a Compound Annual Growth Rate (CAGR) of around 12.35 percent. All these applications provide significant potential for carbon fibre due to the high energy density obtainable as a result of the very high rotation speeds attainable with carbon fibre composite rotors.”
Regan expects that the biggest drivers are going to be acquisition costs and life time value. “The ability of a flywheel to generate energy at higher speeds with less time makes it a reliable and an efficient source of energy with a small environmental footprint, he explained.”
“Though they incur higher installation costs, flywheel energy storage systems require minimal maintenance; they run over a long life span (measured in decades) and are environmentally friendly. New developments in flywheel technology have driven energy storage costs to be very competitive with other energy storage methods however, very high efficiency, compact size and immediate response time to energy demands, make flywheel energy storage systems very attractive.”
“The biggest challenge in designing composite rotors for flywheels is controlling radial stresses,” Regan commented. “Currently most composite flywheels are designed to enforce compressive stress through the thickness to prevent crack formation and composite failure during operation. The energy density of a flywheel rotor is largely determined by the strength and density of its constituent materials.”
“For this reason, carbon fibre composite flywheels can spin at much higher RPMs than metal flywheels can due to their high strength and low weight. High-speed carbon fibre composite flywheels are a good solution for energy storage applications where high power is required for short durations with limited available space.”
“Glass fibre is an alternative material that can be used for lower rotational speed flywheels and hybrid applications with carbon fibre,” he added.
Business intelligence for the fibre, textiles and apparel industries: technologies, innovations, markets, investments, trade policy, sourcing, strategy...
Find out more