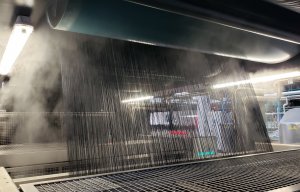
Saitex gets closer to closing the loop
Online garment design, collaboration and the manufacturing of custom garments enabled at scale.
10th March 2021
Innovation in Textiles
|
Los Angeles, CA
The rejuvenation of California’s denim manufacturing industry continues at a pace with the opening of a new plant in Los Angeles by Saitex – the company’s first outside its Vietnam base.
In January, Pakistan-headquartered denim major Artistic Milliners also announced investment in a Los Angeles manufacturing plant.
Los Angeles has long been the denim hub of the USA, but change has been slow to come to the established brands and factories in the region, Saitex observes. The company has installed the latest laser cutting, semi-automated sewing, robotic spraying, 3D laser detailing, and one-step wash machines connected to a state-of-the-art water recycling system at its new LA plant.
It is also initiating an automated supply chain ecosystem using interconnected ordering and costing with shorter lead times and the use of a Cloud-based digital Platform as a Service (PaaS) system will allow a new approach to inventory management and “made to order” capabilities, with, sustainably, and fast.
“Saitex USA is another step in our journey, providing an opportunity to bring sustainable manufacturing and jobs to the United States – a first step in re-evaluating and reinventing global supply chains,” said Sanjeev Bahl, CEO, and founder of Saitex.
With a team led by industry veteran Kathy Kweon as USA president, the company says it has recruited the best of the industry to work at Saitex in Los Angeles.
At its current plant in Ho Chi Minh City, Saitex produces an average of 18,000 pairs of jeans per day and with a $22 million recycling system on-site, water consumption for each pair of jeans has been greatly reduced from 80 litres to just one. With a focus on removing any impact on the outside world, the entire facility in Vietnam is supported by renewable energy sources while minimizing all waste products or reinventing them into materials used to build orphanages in neighbouring cities.
Business intelligence for the fibre, textiles and apparel industries: technologies, innovations, markets, investments, trade policy, sourcing, strategy...
Find out more