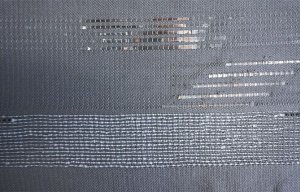
Smart textiles woven on industrial looms
Researchers at MIT incorporated optoelectronic diodes into fibers, which were then woven into washable fabrics.
9th August 2018
Innovation in Textiles
|
Cambridge, MA
Researchers at MIT have embedded high speed optoelectronic semiconductor devices, including light-emitting diodes (LEDs) and diode photodetectors, within fibres that were then woven at Inman Mills, SC, into soft, washable fabrics and made into communication systems.
This marks the achievement of a long-sought goal of creating smart fabrics by incorporating semiconductor devices — the key ingredient of modern electronics — which until now was the missing piece for making fabrics with sophisticated functionality, the team explains.
This discovery, the researchers say, could unleash a new Moore’s Law for fibres — in other words, a rapid progression in which the capabilities of fibres would grow rapidly and exponentially over time, just as the capabilities of microchips have grown over decades.
The findings are described in the journal Nature in a paper by former MIT graduate student Michael Rein; his research advisor Yoel Fink, MIT professor of materials science and electrical engineering and CEO of AFFOA (Advanced Functional Fabrics of America); along with a team from MIT, AFFOA, Inman Mills, EPFL in Lausanne, Switzerland, and Lincoln Laboratory.
Optical fibres have been traditionally produced by making a cylindrical object called a preform, which is essentially a scaled-up model of the fibre, then heating it. Softened material is then drawn or pulled downward under tension and the resulting fibre is collected on a spool.
The key breakthrough for producing these new fibres was to add to the preform light-emitting semiconductor diodes the size of a grain of sand, and a pair of copper wires a fraction of a hair’s width. When heated in a furnace during the fibre-drawing process, the polymer preform partially liquified, forming a long fibre with the diodes lined up along its centre and connected by the copper wires.
In this case, the solid components were two types of electrical diodes made using standard microchip technology: light-emitting diodes (LEDs) and photosensing diodes. “Both the devices and the wires maintain their dimensions while everything shrinks around them” in the drawing process, Rein says. The resulting fibres were then woven into fabrics, which were laundered 10 times to demonstrate their practicality as possible material for clothing.
“This approach adds a new insight into the process of making fibres,” said Rein, who was the paper’s lead author and developed the concept that led to the new process. “Instead of drawing the material all together in a liquid state, we mixed in devices in particulate form, together with thin metal wires.”
One of the advantages of incorporating function into the fibre material itself is that the resulting fibre is inherently waterproof. To demonstrate this, the team placed some of the photodetecting fibres inside a fish tank. A lamp outside the aquarium transmitted music (appropriately, Handel’s “Water Music”) through the water to the fibres in the form of rapid optical signals. The fibres in the tank converted the light pulses — so rapid that the light appears steady to the naked eye — to electrical signals, which were then converted into music. The fibres survived in the water for weeks.
Though the principle sounds simple, making it work consistently, and making sure that the fibres could be manufactured reliably and in quantity, has been a long and difficult process. Staff at the Advanced Functional Fabric of America Institute, led by Jason Cox and Chia-Chun Chung, developed the pathways to increasing yield, throughput, and overall reliability, making these fibres ready for transitioning to industry. At the same time, Marty Ellis from Inman Mills developed techniques for weaving these fibres into fabrics using a conventional industrial manufacturing-scale loom.
“This paper describes a scalable path for incorporating semiconductor devices into fibres. We are anticipating the emergence of a Moore’s Law analogue in fibres in the years ahead,” said Fink. “It is already allowing us to expand the fundamental capabilities of fabrics to encompass communications, lighting, physiological monitoring, and more. In the years ahead, fabrics will deliver value-added services and will no longer just be selected for aesthetics and comfort.”
He says that the first commercial products incorporating this technology will be reaching the marketplace as early as next year. These initial applications will be specialised products involving communications and safety. In addition to commercial applications, Fink says the US Department of Defense “is exploring applications of these ideas to our women and men in uniform.”
Business intelligence for the fibre, textiles and apparel industries: technologies, innovations, markets, investments, trade policy, sourcing, strategy...
Find out more