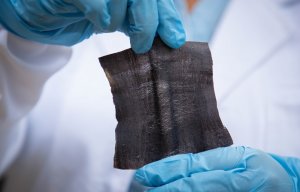
Laser printing produces waterproof e-textiles in minutes
Researchers at the UK’s University of Southampton have revealed plans to develop fabrics for clothing which will generate electricity through wearers’ movement and body heat. It is believed the technology could be used to power personal devices such as MP3 players or wireless health-monitoring systems. The smart fabrics will be made by using rapid printing processes to attach a film of piezoelectric or thermoelectric material to a textile base, which will the
26th August 2010
Innovation in Textiles
|
Southampton
Researchers at the UK’s University of Southampton have revealed plans to develop fabrics for clothing which will generate electricity through wearers’ movement and body heat.
It is believed the technology could be used to power personal devices such as MP3 players or wireless health-monitoring systems. The smart fabrics will be made by using rapid printing processes to attach a film of piezoelectric or thermoelectric material to a textile base, which will then be able to harvest and conduct electricity for potential use.
Team leader Dr Steve Beeby told The Engineer that the project was part of a wider field of research into adding functionality into textiles. “The energy-harvesting project could act as the power supply for electronic functionality that’s also been incorporated into a textile or garment,” he said.
“Alternatively, it could be used as a localised energy generator and store, and then potentially could power or recharge a mobile phone, for example,” Beeby added.
The team will test a range of polymers with piezoelectric properties for the attached film of material, either from the polymer itself or from ceramic powder in the polymer, generating electricity when mechanical strain is applied. According to Beeby, the thermoelectric material will be made from two attached semiconductors (p-type and n-type), which create a voltage by a process known as the Seebeck effect when they are at different temperatures.
“The objective is that it its impact on the fabric is as minimal as possible, so that a nice-feeling, compliant fabric doesn’t become stiff,” said Beeby.
“The challenge is getting the materials to be active enough given that the fabrics are quite difficult to print on. You can’t really heat these textiles up too high but a lot of the processes used at the moment are at several hundred degrees so you have to develop low-temperature versions of the materials,” said Beeby.
Beeby plans to test a range of fabrics including poly-cottons, elastics and heat-resistant fibres such as Kermel. The research is scheduled to last five years and has received a £910,000 grant from the EPSRC.
The Southampton team are involved in a number of other similar research programmes , for example the use of rapid printing to create 2D and 3D sensors on fabrics under the EU Microflex project, and the Bravehealth project to print electrodes onto textiles for medical applications.
Beeby has already made several breakthroughs in the field; notably the invention of a tiny vibration-harvesting generator that is attached to industrial machinery to power wireless sensors, which is being commercially trialled through spin-out company Perpetuum.
Source: The Engineer
Business intelligence for the fibre, textiles and apparel industries: technologies, innovations, markets, investments, trade policy, sourcing, strategy...
Find out more