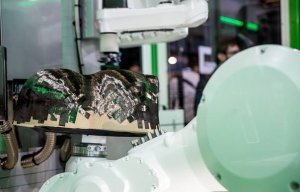
Scalable Samba systems now ready for prepreg
Personal patches could reduce energy waste in buildings, Rutgers-led study says.
8th January 2019
Innovation in Textiles
|
New Brunswick, NJ
Engineers at Rutgers and Oregon State University have found a cost-effective way to make thin, durable heating patches by using intense pulses of light to fuse tiny silver wires with polyester. Their heating performance is said to be nearly 70% higher than similar patches created by other researchers, according to a Rutgers-led study in Scientific Reports.
They are inexpensive, can be powered by coin batteries and are able to generate heat where the human body needs it since they can be sewed on as patches, they add. “This is important in the built environment, where we waste lots of energy by heating buildings – instead of selectively heating the human body,” said senior author Rajiv Malhotra, an assistant professor in the Department of Mechanical and Aerospace Engineering at Rutgers University – New Brunswick. The department is in the School of Engineering.
It is estimated that 47% of global energy is used for indoor heating, and 42% of that energy is wasted to heat empty space and objects instead of people, the study notes. Solving the global energy crisis – a major contributor to global warming – would require a sharp reduction in energy for indoor heating. Personal thermal management, which focuses on heating the human body as needed, is an emerging potential solution. Such patches may also someday help warm anyone who works or plays outdoors.
The Rutgers and Oregon State engineers created flexible, durable and inexpensive heating patches by using “intense pulsed-light sintering” to fuse silver nanowires – thousands of times thinner than a human hair – to polyester fibres, using pulses of high-energy light. The process takes 300 millionths of a second, according to the study funded by the National Science Foundation and Walmart US Manufacturing Innovation Fund.
When compared with the current state of the art in thermal patches, the Rutgers and Oregon State creation generates more heat per patch area and is more durable after bending, washing and exposure to humidity and high temperature, researchers explain.
Next steps include seeing if this method can be used to create other smart fabrics, including patch-based sensors and circuits. The engineers also want to determine how many patches would be needed and where they should be placed on people to keep them comfortable while reducing indoor energy consumption.
Business intelligence for the fibre, textiles and apparel industries: technologies, innovations, markets, investments, trade policy, sourcing, strategy...
Find out more