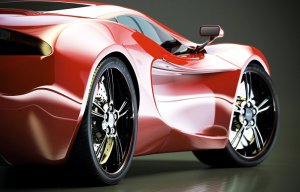
Covestro joins Composite Application Center in Singapore
Stricter import bans have left major cities in Asia in need of viable local textile recycling solutions.
2nd September 2022
Innovation in Textiles
|
Singapore
Royal Golden Eagle, a Singapore-headquartered global group of resource-based manufacturing companies which includes world-leading viscose fibre producers Sateri and Asia Pacific Rayon (APR), is developing urban-fit, closed-loop textile-to-textile recycling solutions.
The newly-formed RGE-NTU Sustainable Textile Research Centre (RGE-NTU SusTex) is a five-year research collaboration between RGE and Nanyang Technological University (NTU), to accelerate innovation in textile recycling that can be deployed in urban settings. It will develop new technologies to recycle textile waste into fibre and create new eco-friendly and sustainable textiles.
This move comes on the back of the tightening of waste import bans in countries such as China, India and Indonesia, which are among the world’s largest waste processors. The stricter import bans have left cities in need of viable local textile recycling solutions to tackle the immense textile waste generated.
“Current textile recycling technologies which rely primarily on a bleaching and separation process using heavy chemicals cannot be implemented due to environmental laws,” said RGE executive director Perry Lim. “At the same time, there is an urgent need to keep textiles out of the brimming landfills. As the world’s largest viscose producer, we aim to catalyse closed-loop, textile-to-textile recycling by developing optimal urban-fit solutions that can bring the world closer to a circular textile economy.”
Globally, an estimated 90 million tons of textile waste is generated and disposed of every year, with less than 1% being upcycled into new clothing or other textile materials. By 2030, the amount of global textile waste, which currently accounts for almost 10% of municipal solid waste, is expected to reach more than 134 million tons.
Downcycling
At present, most of the available textile recycling technologies are open-loop, where textile waste is typically downcycled to lower-quality products – insulating materials, cleaning cloths, etc. – or is used in waste-to-heat recycling.
“Closed-loop textile-to-textile recycling processes, particularly chemical recycling, are still under development,” Lim said. “Scaling up the technologies to industrial scale remains a challenge. A key bottleneck is that refabricating textile waste into fibre needs purity standards for feedstock. However, most of the clothes that we wear are made of a mixture of different synthetic and natural fibres, which makes separating the complex blends of materials challenging for effective recycling.
“Our aim is to address this industry pain point by developing viable solutions that use less energy and fewer chemicals, produces harmless and fewer effluents, and then can potentially scale up across our global operations.”
To tackle the key challenges in closed-loop textile recycling, RGE-NTU SusTex is looking into four key research areas – cleaner and more energy efficient methods of recycling into new raw materials, automated sorting of textile waste, eco-friendly dye removal and the development of a new class of sustainable textiles that is durable for wear and at the same time lends itself to easier recycling.
Technologies developed by RGE-NTU SusTex will be test bedded at RGE’s pilot urban-fit textile recycling plant in Singapore, which is projected for completion as early as 2024. If successful, RGE has plans to replicate the plant in other urban cities within its footprint.
Business intelligence for the fibre, textiles and apparel industries: technologies, innovations, markets, investments, trade policy, sourcing, strategy...
Find out more