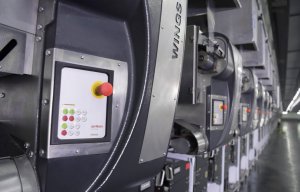
Indian spinner uses WINGS to make rPET FDY
Fibre and spinning preparation stages play decisive roles in final quality.
30th November 2022
Innovation in Textiles
|
Barcelos, Portugal
Valérius 360 and Trützschler have partnered in a pioneering collaborative project to achieve high-quality recycled yarn with the high potential to drive measurable progress towards a more sustainable textile industry.
Headquartered in Barcelos, Portugal, and founded in 2017, Valérius 360 produces yarn by recycling waste from its own spinning and knitting processes. Recently, its experts launched a new project with the aim of increasing the quality of yarn made from recycled waste fibre. Processing recycled fibres, however, is tricky in many ways and reopening textiles down to the fibre leads to a reduction in quality.
Trützschler has the technologies and significant experience to support spinners with applications that involve recycled waste fibres and its experts have a deep understanding of the decisive role that fibre and spinning preparation stages play in the quality of the final yarn.
The team from Valérius 360 wanted to find ways of improving the processes for yarns made from 50% recycled and 50% virgin cotton and in particular, was seeking ways to reduce thick and thin spots, which disturb the appearance of the textile surface.
At the Trützschler Technical Center in Mönchengladbach, Germany, special trials showed that using a direct spinning process for this application delivers much better results than a process with a draw frame passage for rotor yarns.
In direct spinning, the sliver from the card is directly drawn in the draw frame which is integrated in the can stock. This involves one less process step than using an autoleveller draw frame, while also saving space and giving staff more time for other operations.
Direct spinning showed a clear capacity to reduce the number of faults in the yarn. As a result, the yarn breaks were 30% lower and the total imperfections 38% lower. The direct spinning process also has a positive effect on energy consumption – compared to the process with a draw frame passage, for a medium plant size, a savings potential of 5% is achieved with direct spinning. At an energy price of 0.2 €/kW, the savings amount to over €5,000 per year.
The team from Valérius 360 also received in-house training from the Trützschler customer service department. Together, they analysed and significantly improved the process at the Valérius 360 production site. This helped to bring yarns made from recycled raw materials up to 50% – the reference level for yarns made from virgin raw materials. Accordingly, 50% of all yarn producers with raw cotton for rotor yarns and comparable yarn counts produce a poorer quality.
This project shows how customers can improve the processing of recycled materials by using preparation systems from Trützschler. This includes plant concepts for fibre preparation, such as T-Blend or the TC 19iR and also those for spinning preparation like direct spinning with the unique IDF from Trützschler. These systems help customers to maximise the full potential of the material they are processing, because quality is decided in the preparation stage.
“We are very grateful for the great support that Trützschler has given and continues to give us at all levels – from machine configuration through to product development, assembly and customer service,” said Miklós Pál Nagy, Valérius 360 manager.
Business intelligence for the fibre, textiles and apparel industries: technologies, innovations, markets, investments, trade policy, sourcing, strategy...
Find out more