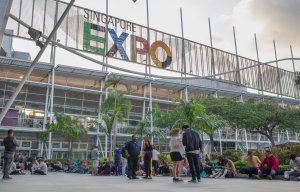
ITMA ASIA Singapore publishes exhibitor list
Opinion
Celebrating milestones already reached, while highlighting opportunities to further accelerate scale-up of material and technology innovations.
30th June 2025
Anne Prahl
|
London
Future Fabrics Expo 2025 (24th and 25th of June, London), which celebrated its 15th anniversary this year, presented an extensive selection of commercially available lower impact materials for fashion, footwear and home products, while showcasing next-gen materials and technologies at various stages of their innovation journey.
Circularity innovation and collaboration
Building on last year’s focus on circular materials and technologies, the Expo’s Re-Solve Lab featured innovations around textile-to textile recycling, utilisation of waste materials and by-products, as well as enabling technologies.
With EU and global sustainable and circular textiles regulations looming on the horizon, investment and scale-up of textile-to-textile recycling technologies are gathering momentum. Represented at the Expo were recycling solutions including Ambercycle, BioCulus and Säntis, as well as material innovations including Circulose, Spinnova and Spiber, which already use, or are planning to use, textile waste as a feedstock.
As discussed during several panels, textile waste has huge potential but the cost of managing it is still prohibitive. Clara Luckner from environmental consultants Systemiq shared that the process to make recycled polyester is estimated to cost up to 2.6 times more than producing virgin polyester in Asia. These figures are based on a study focussing on depolymerisation as part of the chemical recycling process, which was part of Systemiq’s recent report ‘The Textile Recycling Breakthrough’. The report highlights that the business case for textile-to-textile recycling will not work, unless access to feedstock is improved, off-take demand is strengthened, production costs are reduced, and the cost gap is levelled through EPR funding and green premia.
As an alternative to traditional chemical recycling processes, several innovators are working with enzymes to digest and break down specific types of textile waste. Powered by Chinese based recycled material manufacturer REO-ECO, BioCulus enzyme recycling process targets polyester and breaks it down to its molecular building blocks, resulting in virgin-grade rPET chips and yarn.
Another example is Evoralis, an enzyme recycling technology spun out from the University of Cambridge to provide solutions for post-consumer plastics, such as polyester, nylon, and elastane. As explained by the company’s CEO Daniel Kaute, the technology is feedstock agnostic, meaning that it can work on a wide range of feedstock. Kaute further emphasised that feedstock needs to be available locally at the right quantities, as transporting it around the globe is not viable.
There was much talk about the lack of enabling technologies, such as cost-effective textile waste sorting, for the textile-to-textile circle to work efficiently. One such innovation is Fibarcode, an engineered identifier, which aims to provide authentication, traceability and end-of-use data management, while mitigating recycling disruption. The fibre can be embedded into fabric through standard knitting or weaving or utilised as a thread in garment manufacturing and is made entirely from commercially available polymers, including recycled, bio-based, and/or biodegradable materials. This innovation is currently at the experimental and demonstration pilot stage and is actively seeking pilots with interested parties.
While there has been a dramatic increase in textile recycling technologies and recycled materials over the last five to ten years, commercialising these continues to be a slow and difficult journey.
As a result, innovators and industry organisations are exploring different approaches to aggregating demand for specific fibres or technologies to overcome the challenges of high minimums and reducing cost.
This concept has seen the emergence of new collaboration models between stakeholders from the same value chain as well as across value chains and sectors. One example is collaborative innovation platform Fashion for Good’s initiative for so-called ‘Fiber Clubs’, which aim to bring together brands, innovators and manufacturers to enable faster adoption of next-gen materials in the fashion industry. Companies already benefitting from these clubs are US recycling technology innovators Circ, who are currently building their first commercial scale factory in France, backed by the French government, and material science company AltMat, who transform agricultural waste into high-value materials.
Kenji Higashi, Executive Vice president at Japanese biotech company Spiber, talked about the company’s involvement in the BioCircular Materials Alliance, which brings together leading brands, manufacturers, and innovators to accelerate the global transition toward a circular fashion industry. The Alliance has a particular focus on innovative recycling processes designed to transform biological waste materials, including cotton, viscose, and wool, into valuable new materials and is currently working on a project to understand what kinds of dyes and chemical treatments cause problems for recycling. The output will be a ‘Materials Biocircularity Database’, which is intended to support optimised product design and manufacture to enable recycling efficiency at product end-of-life.
Bio- fabricated, recycled and natural colouration
Following on from last year’s spotlight on alternative dyeing methods, the Expo provided another deep dive into existing and emerging colouration methods.
To set the scene, a joint installation from nonprofit environmental organisation Parley for the Oceans and textile company Positive Materials showcased research of bio-fabricated, recycled and natural dyeing technologies, where testing was carried out under real production conditions to demonstrate existing dye capabilities across different fibres and fabrics.
UK biotech company Post Carbon Lab upcycles atmospheric CO2 into colours, dyes, pigments, coatings and finishes using photosynthetic microbes for textile and polymer applications. The company exhibited samples of their collaboration with herbal dye experts True Tone Ink India, as well as their latest samples of bio-based pigments for use in future bioplastics. This project seeks to address the lack of suitable bio-based dyes, as most bioplastics are currently still dyed using synthetic dyes and auxiliaries.
UK-based colour and fibre innovation company DyeRecycle showcased their DyeRecycle Synthetics technology, which recovers and recycles dyes from synthetic textile waste, as well as DyeRecycle Cellulosics, which transforms cotton into a cellulosic powder, which can be used as a pigment for new fabrics. The company also launched their collaboration with Positive Materials with the aim to bring their technology to Portugal’s fashion manufacturing sector for scale-up.
UK material start-up Amphico launched their unique Amphicolour waterless textile colouration process, which involves dope-dyeing yarns in only 6 primary colours, while the use of optimal mixing during the weaving process can create over 10000 colours from these. The company believe that this approach makes dope dyeing scalable, as it dramatically reduces the minimum order barrier.
UK biotech company Modern Synthesis have been showcasing their ground-breaking nanocellulose based innovations for several years now and samples have been presented in limited colours such as off-white or black, as the team wanted to focus on material performance first. To extend their materials’ aesthetic appeal, the company have now started trialling natural and other commercially available pigments, which can be switched out to for replacement by compatible bio-based pigments and dyes, as they become available in the future.
UK platform technology company Sparxell utilise naturally reflective, plant-based cellulose crystals to
produce colourful pigments for a wide range of applications including fashion textiles and packaging. In partnership with Positive Materials, the company has launched cellulose derived textile ink, which can be printed on any knitted or woven cellulose material. The ink will be available commercially from the end of June 2025, with printing orders processed through Positive Materials.
As denim dyeing and manufacturing still causes significant environmental impact, it is imperative to explore new concepts, which may have the potential to disrupt traditional processes. Designer Emily Gubbay’s Infinity Blue is described as a circular colour system that recovers synthetic indigo from denim waste and can be applied to textiles either as a dye or as a pigment in print paste formulations. The extraction process has been tested and validated at lab scale, utilising both pre and post-consumer denim waste.
New Blue by biotechnology company LAB Denim is a patented, indigo-free, digital, post-weave colourisation method, which aims to provide a scalable, sustainable alternative to how denim is currently produced. The digital finishing process recreates wear patterns and aging without harmful chemicals like bleaches or potentially damaging techniques like heat lasers. According to the company, this process is ready to be scaled up into bulk production.
Business intelligence for the fibre, textiles and apparel industries: technologies, innovations, markets, investments, trade policy, sourcing, strategy...
Find out more