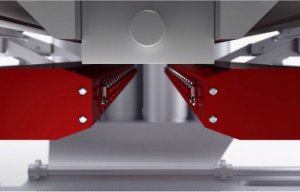
Filtrex Innovation Award shortlist announced
Filtration efficiencies of more than 99.99% easily achieved in typical FFP2 filter media.
10th March 2022
Innovation in Textiles
|
Neumünster, Germany
The new hycuTEC hydro-charging solution for the charging of nonwovens developed by Oerlikon Nonwoven enables filter efficiencies to be increased to more than 99.99% and offers meltblown producers considerable material savings with simultaneously improved filtration.
The hycuTEC is the market’s first industrially-manufactured hydro-charging solution that can be seamlessly integrated into the production process and it is also easily retrofitted to existing systems as a plug and produce component.
HycuTEC hydro-charging can reduce the pressure loss in typical FFP2 filter media to less than a quarter. Filtration efficiencies of more than 99.99% are easily achieved in typical filter media of 35gsm at 35 Pa. Tests at pilot customers manufacturing FFP2 face masks have confirmed quality increases due to the improved filtration with a simultaneous reduction in material usage of 30%. For end users, the consequence is noticeably improved comfort resulting from significantly reduced breathing resistance.
“The hycuTEC process excels as a future-proof technology due to its considerably lower water and energy consumption compared to other hydro-charging concepts,” said Ingo Mählmann, head of sales and marketing at Oerlikon Nonwoven. “This unit allows an additional drying process to be dispensed with in many applications, which has a huge impact on energy consumption.”
The hycuTEC unit can be easily and quickly installed and is simple to operate, set and service, while also being extremely user-friendly.
Whereas classical hydro-charging processes charge the finished nonwoven material, the hycuTEC concept is based on the all-round charging of each filament. Through controlled atomization, a charge is evenly transferred to the fibres from the water spray and a special additive is used to permanently bond the charge to the surface of each fibre. The result is filter media with a uniformly stable charge over the entire cross-section and an effective fibre surface area about 10 times greater than that of surface-charged media. Integrating the new unit into a state-of-the-art Oerlikon Nonwoven meltblown system helps achieve a uniformly high product quality across the whole production process.
Business intelligence for the fibre, textiles and apparel industries: technologies, innovations, markets, investments, trade policy, sourcing, strategy...
Find out more