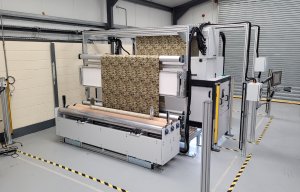
Seeing beyond the patterns
Largest sensor selection on the market.
28th June 2021
Innovation in Textiles
|
Saal/Donau, Germany
Whether woven, knitted or tufted, textile manufacturers must ensure all threads, stitches and patterns are perfectly straight in their finished fabrics, because any distortions will lower the quality and consequently the price attained for them.
Mahlo, based in Saal/Donau, Germany, has the largest sensor selection on the market designed to ensure any such distortions are reliably detected and removed at today’s standard fabric speeds, regardless of technical properties, haptics or appearance.
“We give manufacturers the right tool to evaluate and monitor the condition of their fabric,” says Stephan Kehry, textile product manager at Mahlo. “Only with distortion detection that is optimally suited to their own product mix can they meet the increasing demands of the market.”
Optoelectronic
For the majority of textile manufacturers, the solution for straight goods is optoelectronic scanning.
“No other measuring principle can cover so many materials and applications fully automatically,” says Kehry. “Developed by company founder Heinz Mahlo, the principle continues to set standards in the field of distortion detection today. Continuous further development and digital technology make it possible to stay one step ahead of the ever more complex textile structures. Our TK-12 sensor is capable of detecting weft and course distortion in virtually all textile structures and to determine the total distortion reliably and in real time.”
This is achieved by using a suitable number of sensors that are evenly distributed across the fabric width. They detect and calculate the warpage in real time using an oscillating lens that registers the light-dark modulation. As a result, distortion is detected simultaneously across the entire width of the fabric. Distortion changes, such as in a seam, can be reacted to without delay, either by an automatic straightening machine or the operator.
Imaging scanning
For the few materials that cannot be scanned with the TK-12 optoelectronic sensor, Mahlo uses imaging scanning as a supplement.
“These exceptions are fabrics in which there is little pronounced light-dark modulation, due to low fabric speeds and yarn counts, or low yarn frequency, for example,” Kehry explains. “The imaging method is also the best option for manufacturers of woven crepe, certain blackout fabrics, fabrics with untwisted weft, or structures with small patterns.”
The course of the weft and warp threads is recorded by a high-resolution area scan camera with an imaging area of 4x3cm. An intelligent algorithm in the software evaluates the captured image and determines the degree of distortion.
Hybrid scanning
It is also possible to combine the best of both worlds with both optoelectronic and imaging scanning.
“Hybrid scanning combines the advantages of both systems to take a lot of work off the manufacturer’s hands,” Kehry says. “This is because, depending on the material type of the goods passing through, the software independently selects which warpage detection generates the most stable evaluation. Especially with a wide product range with frequent fabric changes, hybrid scanning brings many benefits.”
Special circumstances also require special measures.
“Carpets, for example, have a very low weft or tufting row density due to their mostly coarse yarn qualities,” says Kehry. “At the same time, fabric speeds on most coating lines are relatively low. For these special conditions, Mahlo has developed its own camera sensor that covers a significantly larger area during scanning and thus makes coarse cross structures visible.
“There are also a few textiles, for example patterned woven and knitted lace or terry fabrics, which are extremely difficult or impossible to scan with conventional technology and therefore cannot be accurately straightened. For these applications, straightening according to the weft thread is either not practical or not possible, but of course, manufacturers of these fabrics also want straight.”
To detect the warpage value of these products and successfully straighten them, Mahlo uses the camera-based Patcontrol PCS-20, which with special software can detect, evaluate and record several parameters of a fabric web, including skew and sheet distortion, longitudinal and cross repeat, and fabric width.
Business intelligence for the fibre, textiles and apparel industries: technologies, innovations, markets, investments, trade policy, sourcing, strategy...
Find out more