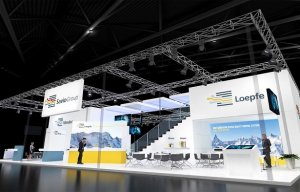
Loepfe quality control solutions on show at ITMA Asia
Loepfe Brothers reports that it experienced very strong demands for its WeftMaster FALCON-I yarn control solution.
8th June 2018
Innovation in Textiles
|
Wetzikon, Switzerland
The market for technical textiles has been steadily growing for several years now. Typical applications include the production of fabrics for airbags, tyre cords, filtration materials, architectural fabrics and sailcloth. The quality requirements for many of these fields – especially for safety-critical applications – are very high and the challenge for weaving mills is production with zero-defects.
During the Techtextil North America show, which was held in Atlanta, Georgia, USA, at the end of May, Loepfe Brothers reports that it experienced very strong demands for its WeftMaster FALCON-I yarn control solution.
Quality sensitive applications
In quality sensitive applications, even the smallest knots, fluff, filamentation, thick places and capillary breaks must be eliminated before being woven into the fabric. To monitor such unwanted yarn faults on the running threads, the WeftMaster FALCON-i is installed before or after a weft feeder.
The yarn control system ensures reliable control of latest high-tech materials such as carbon fibres, monofilaments and multi-filaments as well as spun yarns in any material composition. Even conductive yarns can be processed without any restriction, the company reports - the sensor works reliably with coloured yarns and measures unaffected by vibration. Static electricity or electromagnetic fields also have no influence on the results, as the sensor housing is made from shielding material.
Sensitivity level
The sensitivity level of the FALCON-i can be set either manually or automatically. The thread to be monitored is guided through the optical measuring field by yarn guides placed before and after the sensor virtually contact-free. An output signal triggers the required action, as soon as a defect has been detected. The microprocessor-controlled sensor provides many options for connection to machine controls. Additionally, the weft sensor function can be integrated into FALCON-I, which allows elimination of a further yarn guiding contact before the fabric production.
Loepfe’s optical yarn defect sensor FALCON-i not only complements the various available knotless weaving concepts, but can also be used in many different processes in the textile production chain, wherever individual yarn monitoring should ensure quality.
Business intelligence for the fibre, textiles and apparel industries: technologies, innovations, markets, investments, trade policy, sourcing, strategy...
Find out more