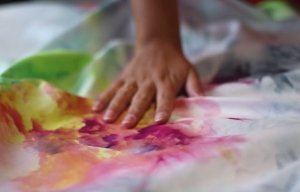
SPGPrints’ rotary screens and digital inks at ITMA
From 20-26 June, Schwing experts will discuss the potentials and advantages of the company’s systems and cleaning shops.
3rd May 2019
Innovation in Textiles
|
Neukirchen-Vluyn
Schwing vacuum pyrolysis system Vacuclean. © Schwing Technologies
Leading German specialist Schwing Technologies will be presenting thermal cleaning solutions for polymer-contaminated production tools at this year’s ITMA 2019 in Barcelona. From 20-26 June, Schwing experts – Managing Director Thomas Schwing and Head of Sales Virgilio Perez Guembe – will discuss the potentials and advantages of the company’s systems and cleaning shops.
The manufacturer has been an internationally successful specialist for polymer removal for 50 years. Since the beginning of 2019, American and Canadian customers have also benefited from the service and advice of US-experts Schwing North America Technologies, based in Princeton, NJ.
The energy-efficient, environmentally friendly and fully automatic systems Vacuclean and Innovaclean are designed to guarantee residue-free cleaning results. Upon request, Schwing can expand these systems with additional post-treatment units.
Schwing fluidised bed system Innovaclean. © Schwing Technologies
“The easy-to-install systems remove any polymer residues from production tools reliably and gently,” said Thomas Schwing, Managing Director of Schwing. These include spin packs or spinnerets, filter discs or filter bundles as well as melt-blown and spunbond dies with lengths of up to six meters. The advantages for the producing technical textile and clothing industry are shorter machine downtimes and a longer service life of the cleaned parts, the company reports.
In order to save time and costs, predictive maintenance also plays an increasingly important role in thermal cleaning. With immediate effect, the German specialist is equipping all new Schwing systems with components that support predictive maintenance of the systems. This includes components such as new fault reporting concepts, an internal data link for data mining and digital plant documentation in a Schwing cloud.
“We attach great importance to predictive maintenance,” explained Virgilio Perez Guembe, pointing out that all equipment relevant data is written down and recorded during the process. Customers benefit from the electronically generated equipment documentation, which guarantees uncomplicated use of the data. “Our in-house Windows app Schwing DataAnalyser helps to evaluate this data, to check the system and thus supports the predictive maintenance of the systems.”
On request, Schwing can modernise older systems for customers at its headquarters in Neukirchen-Vluyn.
Business intelligence for the fibre, textiles and apparel industries: technologies, innovations, markets, investments, trade policy, sourcing, strategy...
Find out more