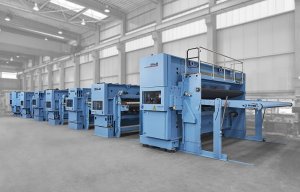
Huafon Microfiber to install four more lines from DiloGroup
Megatrends, such as urbanisation and the economic situation, are driving factors for the continued growth of geononwovens.
27th March 2018
Innovation in Textiles
|
Albstadt
Megatrends, such as urbanisation and the economic situation, are driving factors for the continued growth of geononwovens. According to a recent study, 682,000 tons of geononwovens were produced in 2014, and a production quantity of 943,000 tons is expected for 2020. This corresponds to a total annual growth of 38% over six years.
Groz-Beckert has conducted a series of tests to analyse the impact of the needle's working part geometry on a textile’s physical properties, depending on the fibre orientation and the needling parameters of nonwovens.
“Here, a particular focus was placed on the application of the geononwovens. Geotextiles must fulfil several requirements simultaneously. Separation, filtration and draining are among its task, whereby the mechanical stress usually tests the limits of its capacity. The geotextile robustness classes dictate what a geotextile can ultimately withstand,” said the company. The following tests are required for nonwovens: determining the mass per unit area in accordance with DIN EN ISO 9864; and measurement of the stamping puncture force based on tests in accordance with DIN EN ISO 12236.
“The measurement values enable the geotextiles to be allocated to the robustness class. Depending on the type of geotextile, we differentiate between five different robustness classes – from GRC 1 to GRC 5,” the manufacturer explained. “Nonwovens in geotextile robustness class 5 must have a fabric weight of at least 300 gsm and a stamping puncture force of at least 3.5 kN. In order to take into account the production-related product deviations, the requirements always refer to the 5% minimum quantile.”
In sections of the geotextile spectrum, Groz-Beckert customers work with Tri STAR and Cross STAR felting needles, as the surface quality plays a secondary role, but high tensile strengths are required in the product. Tri STAR needles have concave sides and Cross STAR needles have an additional forth edge. Both working part cross-sections were compared with a standard triangular working part in the test series.
In order to correspond to at least robustness class 5, a nonwoven with a fabric weight of 320 gsm was produced. The web formation took place with 90 mm long polypropylene staple fibres with a fineness of 4.4 dtex. The draft in the web drafter VST19 was set at 40%.
The pre-needling took place on a Di-Loom OD-II 20 with Gebecon needles. The stitch density was set to 75 S/cm² and the penetration depth was set to 10 mm. The main needling on a Di-Loom OUG-II SB 15 took place with all three working part cross-sections, always with a stitch density of 250 S/cm², in tandem operation. The penetration depth was set to 8 mm.
This series of tests showed the impact of the working part geometry of felting needles on the physical textile properties of geononwovens. All nonwovens created during the test with a penetration depth of 8 mm achieved the robustness class 5. Tests with a 50% increase in the penetration depth (12 mm), show a significant drop in puncture force, meaning that only a lower robustness class could be achieved here.
A direct comparison between the three different working part geometries generally shows that the Tri STAR and Cross STAR felting needles, compared with the standard triangular working part achieve a higher product density with the same machine adjustment, achieve better tensile strength properties and a higher isotropy, and offer a higher stamping puncture force.
“Based on these results, we can say that using Tri STAR and Cross STAR felting needles reduces the amount of raw material required with the same mechanical properties. Using the correct felting needles therefore has a significant impact on the material costs and, as such, directly on the manufacturing costs,” the company concluded.
Business intelligence for the fibre, textiles and apparel industries: technologies, innovations, markets, investments, trade policy, sourcing, strategy...
Find out more