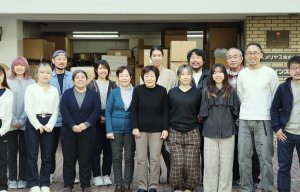
Pathway to GOTS for smaller operators
Versatility of warp knitting offers high potential for the incorporation of electronic circuits based on conductive yarns.
6th April 2021
Innovation in Textiles
|
Online
The benefits of the warp knitting process for the creation of electronic textiles (e-textiles) were outlined by Tony Hoojimeijer, president of Karl Mayer North America, during the latest Techtextil and Texprocess North America webinar.
“When considering the e-textiles market it’s clear there are a number of barriers,” he said during the event, first broadcast on March 25th. “Typically, process costs are very high for such products that come onto the market, because producing e-textiles can be a pretty complex process with add-ons for the sensors always demanding multi-step processes. On the user side, washability can then be an issue, as can wearing comfort.
“The way to address this is firstly to find a suitable production process that is very volume oriented and then reduce the production steps for the different components required, to help in terms of costs. Building the functionality into the fabric, instead of adding it to the fabric later, results in more wearable and attractive garments that will lead to better and higher customer acceptance. This is what the warp knitting route offers.”
Complex structures
Warp knitting, he explained, is very different to weaving in the complex structures it can create.
“The whole process works in the warp direction and all the yarns are fed from beams in parallel and then subject to all kinds of intricate movements from the bars,” he said. “Loops are produced which inherently have four-way stretch, which in terms of wearability comfort is a major benefit, and it’s possible to feed many different yarns into the same knitting area, in order to create applications with different characteristics. This is why warp knitting has been successful in so many fields.”
The major markets for warp knits primarily based on polyester and polyamide yarns, include sportswear and intimate apparel, where stretch and comfort are prerequisites. Other big markets are in shoe uppers as well as automotive headliners and many seat components. The medical field is also an area where products such as artificial blood vessels have been produced in a single pass with a warp knitting machine.
Versatility
As far as e-textile are concerned, Karl Mayer developers have already made fabrics in which four separate electronic circuits based on conductive yarns – treated just as normal yarns – have been knitted into a fabric during single step production.
Hoojimeijer emphasised the versatility of warp knitting in terms of accommodating many different yarns and creating unlimited structures.
In terms of productivity, he explained, fabrics that are 200 inches wide can contain 30 needles per inch operating at 3,000 rpm for 6,000 stitches in parallel.
“Complex arrangements can be fed by different bars in different ways for patterning e-textiles with different functional yarns at specific places, as is typical in athletic shirts which have patterns where things are tighter or looser, with defined areas of compression,” he said. “String bars can place specific conductive yarn patterns in spots throughout the fabric which can combine to create very intricate patterns and this is all done on the fly.”
Demonstrator products produced by Karl Mayer include a remote control sleeve with a sensitive surface for controlling a small robot and a knitted wireless cell phone charger. At ITMA 2019 in Barcelona, a sports shirt for measuring heart rate, temperature and humidity with textile sensors was showcased.
“We have already tested many conductive yarns during development work, and we have a wide range of machines on which to explore potential applications,” Hoojimeijer said in conclusion. “If specific yarns are too thick or rigid, they may be unsuitable, and for specific applications modifications of a machine’s feeding devices or tension controls may be necessary but this is a versatile route to successful mass production for many new e-textile products.
As the largest manufacturer of warp knitting machines in the world, Karl Mayer has recently added an established range of flat knitting technologies with the acquisition of Stoll and is very active in application development to help its customers develop new products, with R&D centres in Germany, Italy and Japan, as well as the USA.
Business intelligence for the fibre, textiles and apparel industries: technologies, innovations, markets, investments, trade policy, sourcing, strategy...
Find out more