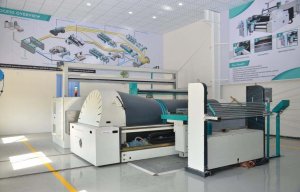
Karl Mayer reinforces its services in India
A demo centre featuring the Isowarp as its centrepiece is set to open at the site in Ahmedabad.
23rd April 2021
Innovation in Textiles
|
Ahmedabad, India
In Spring 2015, Karl Mayer celebrated the start of production at its new plant in Ahmedabad in India and also launched its new Isowarp sectional warping machine.
A few years later, the Indian factory took over the construction of the Isowarp for the local market, to enable the shortest possible delivery times, the highest availability of spare parts and the best service quality, combined with all the design, quality assurance and product management expertise the entire Karl Mayer Group has to offer. Key component parts also come from the European network to ensure the highest product quality.
The first two models were delivered to Rajapalayam Mills in 2019 and are performing well.
“These machines are working at highest production and produce high quality warp beams, enabling the successful performance of our weaving machines,” says Mohana Rengan, Rajapalayam chief operating officer. “The Karl Mayer Isowarp made in India is real value for money and is on par with the machines made in Germany,”
A demo centre featuring the Isowarp as its centrepiece is now set to open at the site in Ahmedabad where customers can carry out specific processing tests.
The Isowarp sectional warping machine complements the premium Prowarp version as a model suitable for the commodity market. Since its launch, it has been continuously adapted along with the associated GH creel in terms of structure and complexity to meet local conditions and diverse customer requirements. Today, a complete family of machines is on offer. The main additions are versions offering new working widths and performance characteristics relating to beaming tensioning and warping speed, for example, which open up completely new applications. Initially designed for shirt production, the Isowarp can now also be used for household textiles and terry cloth, as well as for processing filament yarns.
Warp preparation productivity can be significantly increased compared to equipment using conventional counterparts. The quality of the warp beams meets the same high standards as all Karl Mayer machines, enabling an efficiency increase in the weaving mill of 2-6%, with high-precision band structure control managed by state-of-the-art software. The Isowarp requires almost no maintenance and only a few spare parts.
Business intelligence for the fibre, textiles and apparel industries: technologies, innovations, markets, investments, trade policy, sourcing, strategy...
Find out more