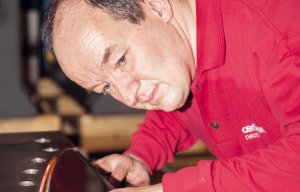
Essential maintenance of meltblown machines
Thermal cleaning ensures nonwoven production for respirators and medical protective clothing
14th April 2020
Innovation in Textiles
|
Neukirchen-Vluyn, Germany
Vacuclean vacuum pyrolysis system from Schwing Technologies removes polymer residues from spin packs, spinnerets as well as melt-blown and spunbond dies with lengths of up to six meters by thermal vacuum cleaning. © Schwing Technologies.
Production lines for nonwovens are running at full speed worldwide. In these times of the coronavirus pandemic, the material is urgently needed for the production of medical textiles. “There is a shortage of masks, surgical or protective gowns everywhere. In order to secure the production processes of nonwovens and supply of medical protective material, precise working machine parts are critical. It is therefore essential to reliably clean the polymer-contaminated tooling and return them to the production process quickly,” says equipment manufacturer Schwing Technologies.
"More than ever before, we have to use our know-how to reduce machine downtimes with short cleaning times and make tools available again quickly," emphasizes Thomas Schwing, Managing Director of German company.
The equipment manufacturer specializes in thermal cleaning systems for machine parts such as spin packs, spinnerets up to six metres long or melt-blown and spunbond dies. In addition to PET, PP and PE, other polymers are also removed using its systems. At the NRW headquarters in Neukirchen-Vluyn, Schwing also cleans process components as a 24/7 service provider, supplementing its service with the corresponding logistics.
In order to accelerate the cleaning of machine components in nonwoven production, the Schwing development team has optimized its ultrasonic cleaning process. Thanks to the new two-side sound, even large machine parts no longer have to be manually turned, Schwing says. This saves time and, above all, manpower. In addition to a thermal vacuum pyrolysis system, the company uses other post-treatment equipment, including ultrasonic cleaning systems.
Previously, this process required two steps, explains Schwing: "What's new is that with two-side sound, the time-consuming turning of machine parts is no longer necessary. Savings in personnel costs, rapid use of tools and reduced machine downtime are the advantages, the expert knows. At the same time, the process minimizes the risk of damaging dies. The entire process, which takes about 8-12 hours, includes several cleaning steps: These imply thermal polymer removal as well as subsequent high-pressure and ultrasonic cleaning. The final drying phase is followed by a final inspection.”
Functional principle of thermal vacuum pyrolysis: The cleaning process takes place in an electrically heated vacuum cleaning chamber. The temperature is measured directly at the machine parts, which are initially heated slowly and particularly gently. Here, a large part of the adhering polymer melts off and flows out. The decomposition of the remaining material takes place at approx. 450 degrees Celsius - remaining carbon is finally removed by adding air (oxidation). © Schwing Technologies.
Schwing offers its customers complete cleaning services at the company headquarters in Neukirchen-Vluyn. This includes disassembly, thermal cleaning and, depending on the component size, post-treatment and inspection. The systems run around the clock 24/7 at the location on the Lower Rhine. Seven specialists contribute their entire know-how and experience from many years of cleaning very sensitive parts reliably and without residue. In addition, four drivers work up to ten hours a day to collect contaminated tooling and return the clean components to customers throughout Germany and neighbouring countries.
Further information is available at: https://www.thermal-cleaning.com/en/cleaning-services-247.html
Business intelligence for the fibre, textiles and apparel industries: technologies, innovations, markets, investments, trade policy, sourcing, strategy...
Find out more