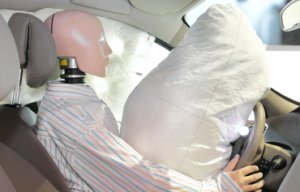
Lectra supports automotive supplier’s airbag operations launch
UTT has also expanded its production capacity for technical dobby and jacquard fabrics with an additional production building with new weaving machines
20th July 2020
Innovation in Textiles
|
Krumbach, Germany
UTT, a subsidiary of the Thai chemical group Indorama Ventures (IVL), and renowned manufacturer of technical fabrics, has recently installed a state-of-the-art textile finishing line for airbag fabrics.
The original UTT weaving mill was founded at its current location in Krumbach, Germany, way back in 1850. Over the years the UTT’s manufacturing focus has shifted from initial production of parachute fabrics to that of technical textiles and especially airbag fabrics. Making airbags is a multi-stage, precisely coordinated complex process, ranging from warp production to laser cutting and UTT's own high standards demand the highest quality, finished with state-of-the-art technology.
In order to develop its key role in this important and innovative market of the automotive industry, UTT has significantly expanded its production capacity for technical dobby and jacquard fabrics at the Krumbach site. Not only was an investment made in an additional production building with new weaving machines, but also one of the world's most modern and innovative textile finishing lines for airbags has recently been installed. UTT chose two very experienced and reliable partners for this project - two German, owner-operated machine and plant manufacturing companies, Menzel in Bielefeld and Brückner in Leonberg. Together with UTT's project managers, the requirements for the line were refined and developed by the experienced technologists of all three companies.
The successful cooperation is based on the specialization of Menzel and Brückner to work out and implement individual customer-oriented solutions. The challenge here is to implement the multiple technical requirements of the line concept. The aim of this project was the production of a high-performance airbag OPW fabric. Therefore, a new process for the multi-stage in-line finishing of OPW fabric was developed, Brückner explains.
For continuous production, the line is equipped with the necessary elements for non-stop fabric change over. Brückner's stenter system is equipped with a newly developed indirect gas heating system. This system completely separates the circulating air of the dryer from the hot burner exhaust gases so that no contact between the sensitive fabric can occur.
In addition, the system has an integrated heat-recovery system for heating up fresh air in order to achieve the highest possible energy efficiency. This heat-recovery system enables a saving of approximately 30 m³ of natural gas per hour for the entire system and significantly reduces CO2 emissions compared to other systems.
The stenter has a horizontal return, low-lubrication fabric transport chain, which is equipped with width tension sensors. With the help of these sensors the fabric tensions occurring in the production process are controlled to ensure that the fabric does not exceed its quality critical parameters. If the pre-set tension values are increased, the machine will react and alter the fabric width accordingly. The process control system allows continuous monitoring of all relevant parameters and data exchange with the customer's own PDA system.
The realization of this innovative system was a demanding challenge but also a very successful cooperation of all participating companies. Together, a common success could be implemented according to the motto ‘Quality Made in Germany’ Brückner concludes.
Business intelligence for the fibre, textiles and apparel industries: technologies, innovations, markets, investments, trade policy, sourcing, strategy...
Find out more