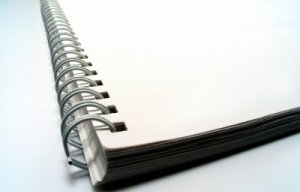
Five students to be recognised for their high-tech solutions at Techtextil
Opinion
The tenth VDMA web-talk held on December 2nd, featured three companies providing essential services to the technical textiles and composites sectors.
17th December 2020
Adrian Wilson
|
Frankfurt, Germany
The textile machinery branch of Germany’s VDMA, the Frankfurt-headquartered mechanical engineering industry association, has held no less than ten webinars showcasing the technologies of some 30 of its members since June this year. Many of the broadcasts have understandably concerned the sudden demand for PPE in 2020, while a second focus has been on achieving savings in energy, water and raw materials.
The latest, however, held on December 2nd, featured three companies providing essential services to the technical textiles and composites sectors.
Georg Sahm
Winding solutions specialist Georg Sahm was planning to mark its 75th anniversary this year by inviting customers and suppliers from around the world to a celebration at its HQ in Eschwege, but instead has had to learn how to do things differently. Based on overcoming the challenges it has faced, Sahm has now established a services platform for digital solutions, such as a video factory acceptance procedure, as well as frameworks for remote installations and support.
The company’s winders and automated bobbin handling systems are designed for effectively dealing with high performance fibres such as aramids, ultra high molecular weight (UHMPW) polyethylenes like Dyneema, Vectran fibre, which is spun from a liquid-crystal polymers (LCPs), glass, PTFE and PVA coated yarns, and especially carbon.
These fibres form the basis of products such as bulletproof vests, helmets and other personal protection equipment, as well as automotive components.
In addition, the company, which is part of the Starlinger Group, produces special winders for monofilaments and tapes for end-use applications such as carpet backing and artificial turf, geotextiles, filters, sun shade fabrics and nets.
The metal strips in an estimated 90% of all the bank notes in the world are meanwhile produced on Sahm parallel winding systems, and other end-use markets include the cable and wires, packaging and automotive sectors.
High strength fibres
Business development manager Bena Manasieva Cavus said that effective winding is an essential component in the high speed production of such high strength fibres, with each specific fibre requiring special attention and having certain weaknesses.
“Aramid is not strong against UV for example, and Dyneema doesn’t like water,” she said.
To compensate, Sahm has developed the YarnStar 3+ system for the high speed unwinding, coating, cooling and winding to add functionality such as hydrophilic/phobic, antibacterial or flame retardant properties, colour flexibility and softness/hardness.
The company has been long established in the processing of carbon fibres for the composites industry, with solutions for PAN precursor yarns, carbon fibres, prepregs and towpregs.
Herzog
Consequently, Sahm frequently partners with Oldenberg-based Herzog, which is a global leader in the braiding technologies which are employed widely in the creation of ‘near net shape’ carbon preforms – 3D textile structures as close to the shape of the final finished component as possible – with key customers in the automotive industry including BMW, Mercedes and Porsche. Suppliers to Airbus and Boeing are likewise partners for aerospace components.
Herzog managing director Janpeter Horn said that while braiding looks complicated, it is really quite simple, involving the building up of three, four or more yarns in oblique directions to their edges. It can be likened to a Maypole system.
“It’s a two-step process exploiting centrifugal forces to create structures with unique characteristics, which can have high flexibility and high torsion stability under load,” Horn said. “The fibres are secured by interlocking with equal load division throughout the length of product in both biaxial and triaxial configurations. There are so many markets for these braided products that we have delivered more than 550 types of customised machine to over 60 companies.
In addition to composite preforms, two other key growth areas for braided textiles are ropes and medical products.
Weight savings
“The ability to replace steel with high strength fibres such as aramids, Dyneema and Vectran has resulted in ropes that have 75% less weight with all of the advantages that brings in terms of towing, mooring, anchoring and lifting and lowering,” said Dennis Behnken. Herzog’s head of sales. “In addition, ropes made from these fibres have ten times the working life of steel equivalents.”
To further enhance high strength fibre braided ropes, Herzog has developed a temperature-controlled heatsetting unit which can be integrated directly into its braiding lines to further enhance the physical properties of the rope structures.
In medical products such as sutures, artificial ligaments and stents, braided fabrics are increasingly the preferred choice for their flexibility in terms of the customised shapes and patterns that can be achieved and the specialised fibres that can be accommodated.
“Our body is like a car,” said Horn. “You can replace or repair more or less every part and there are lots of applications where textile processes
Like Sahm, Herzog has been challenged during 2020 to rapidly develop new digital solutions based on remote installations, as well as virtual trips by customers to its Oldenberg HQ.
Karl Mayer
As the leading manufacturer of warp knitting machines and now, following its acquisition of Stoll, of flat knitting machines, Karl Mayer’s Technical Textiles business unit continues to expand its portfolio.
The company’s weft insertion machines exploit a three yearn system in which weft and warp yarns are held together by a knitting yarn, with all laid straight, without crimp. These high productivity machines can be delivered in widths of up to 6.8 metres and can accommodate a wide variety of yarns, from polyester through t glass, carbon, basalt, etc.
Typical applications for the fabrics produced on these machines include cut-protection fabrics, coated substrates for advertising, glass fibre fabrics and plaster grids for the construction industry, roofing substrates and geotextiles.
NCF (non crimp fibre) systems are biaxial or multiaxial machines in which the orientation within the yarn layers is optimised for maximum reinforcement in fabrics for composites based on glass and carbon.
Spreading
The company’s fibre spreading units were introduced a few years ago in response to the carbon fibre industry’s development of high tow carbon fibres consisting of up to 50,000 filaments in a fibre bundle.
“Carbon fibre is very expensive and these fibres are much cheaper, but compared to traditional 6k and 12k fibres they have some disadvantages,” said sales director Hagen Lotzmann. “They are heavier and it is more difficult to impregnate them with resins. Our spreading units turn them into unidirectional tapes which makes them easier to impregnate, but also significantly lowers their aerial weight for the final application. The carbon tapes are then further processed on our multiaxial machines.”
In a further development of this spreading technology, at ITMA 2019 in Bareclona Karl Mayer introduced a spreading machine with an integrated impregnation unit to produce continuous fibre reinforced thermoplastic tapes.
“Unlike our other machines which are producing fabrics which then have to be further coated or cut and shaped, this machine produces a semi-finished product,” Lotzmann said. “Such composite parts based on tapes are now employed in a wide number of industries including aerospace, automotive, industrial pipes, marine and sporting goods. We have sold the most machines for composites to the wind power sector, but increasingly we are involved in the development of customised solutions with customers who are looking for diversification, and to enter into niche, higher margin markets.”
Business intelligence for the fibre, textiles and apparel industries: technologies, innovations, markets, investments, trade policy, sourcing, strategy...
Find out more