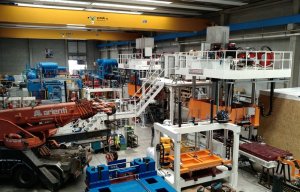
Major European order for Cannon
Japan’s Teijin announced today that it has established the world’s first mass production technologies for carbon fibre reinforced plastic (CFRP), achieving a significant reduction of the cycle time required for moulding car cabin frames to less than one minute. Teijin says that the breakthrough overcomes one of the biggest challenges in the industry and represents a long stride toward the use of carbon fibre for the mass production of cars and other products. Teijin’s
9th March 2011
Innovation in Textiles
|
Tokyo
Japan’s Teijin announced today that it has established the world’s first mass production technologies for carbon fibre reinforced plastic (CFRP), achieving a significant reduction of the cycle time required for moulding car cabin frames to less than one minute.
Teijin says that the breakthrough overcomes one of the biggest challenges in the industry and represents a long stride toward the use of carbon fibre for the mass production of cars and other products.
Teijin’s new technologies include intermediate materials made of thermoplastic resin instead of conventional thermosetting resin for moulding-use CFRP. The company has also developed technologies for welding thermoplastic CFRP parts together and for bonding CFRP with materials such as steel, both of which will help to reduce the use of metal in manufacturing processes.
Going forward, Teijin says it intends to develop mass production applications for CFRP in cars and many other items that require certain levels of structural strength, such as machine tools and industrial robots.
By impregnating carbon fibre with thermoplastic resin, Teijin has developed three intermediate materials for the production of CFRP suited for use in mass-production vehicles. The materials can be used selectively depending on the required strength and cost of the part, and they can be made with various thermoplastic resins, including polypropylene and polyamide. The new intermediate materials are as follows:
- Unidirectional intermediate: ultra high strength in a certain direction.
- Isotropic intermediate: optimum balance of shape flexibility and multidirectional strength.
- Long-fibre thermoplastic pellet: high-strength pellet made from carbon fibre, suited for injection moulding of complex parts.
Using these new intermediate materials, Teijin developed its new technologies for the high speed press moulding of CFRP and the technology is said to be simpler than conventional methods. In addition, Teijin has also developed technologies for welding thermoplastic CFRP parts together, and also for bonding CFRP with materials such as steel.
To demonstrate its new cutting-edge technologies, Teijin has developed an electric-vehicle (EV) concept car that features a cabin frame made entirely from thermoplastic CFRP and weighing only 47 kilograms, or roughly one fifth the weight of a conventional automobile’s cabin frame. The four-seat EV, which is said to be capable of speeds up to 60 km/hour and has a cruising range of 100 km, embodies Teijin’s vision of super-lightweight EVs made with CFRP.
Teijin will use the concept car to introduce its technologies to car makers and parts suppliers, and also to promote joint initiatives to develop lighter cars. Teijin also aims to establish new midstream and downstream business models for its carbon-fibre composites business by supplying CFRP parts to the market.
“With automotive exhaust regulations becoming increasingly strict, there is a mounting need to reduce vehicle weights by using materials such as CFRP, a lightweight material that can be used for many components made conventionally with steel or aluminium”, Teijin said in a statement today.
The Teijin Group, which has identified cars and aircraft as one of its key growth markets, has been developing CFRP for such applications through collaboration between the Teijin Composites Innovation Center and Toho Tenax, the core company in the group’s carbon fibres business.
“Conventional CFRP utilizes thermosetting resin and requires at least five minutes for moulding, so it is not suited for mass production applications that require moulding within about one minute, such as the production of general-purpose cars. This is why CFRP has been limited to use in high-end vehicles”, Teijin adds.
Looking ahead, the Teijin Group aims to accelerate its expansion of advanced composite materials, one of the pillars of the group’s long-term growth strategy. To this end, Teijin will establish a new business group, named the Carbon Fibers and Composites Business Group, by integrating its current business units for carbon fibres and composite materials.
Business intelligence for the fibre, textiles and apparel industries: technologies, innovations, markets, investments, trade policy, sourcing, strategy...
Find out more