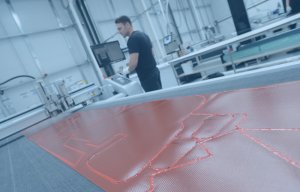
$6 million dollar LEAP for Velocity
3D woven composites are used to manufacture the fan blades, fan case and spacers of the highly successful LEAP engine.
1st December 2021
Innovation in Textiles
|
Albany, NY, USA
Paris-headquartered Safran Aircraft Engines has extended its partnership with Albany Engineered Composites to 2046 as the two companies continue to work together on the next generation engines and contribute to the 2050 net-zero CO2 emissions commitment of the aerospace industry.
The companies signed the original framework agreement in 2006, resulting in the creation of their joint venture for the development of high technology composite parts – 3D woven and resin transfer moulded technologies – designed for aircraft engines, landing gear and nacelles.
3D woven composites play a key role in improving the performance of the latest generation LEAP engine of CFM International, which powers the Airbus A320neo, Boeing 737 MAX and Comac C919 aircraft families.
The advanced material is used to manufacture the fan blades, fan case and spacers of the LEAP engine, leading to significant weight savings and contributing to reduced fuel consumption and CO2 emissions of 15%. Safran and Albany have also teamed-up to work on the development and production of the GE9X 3D composite fan case for the Boeing 777X.
In order to address unprecedented LEAP production ramp-up, the partners have built three state-of-the-art production plants in Rochester, New Hampshire, Commercy, France, and Querétaro, Mexico. These three sites have delivered more than 130,000 parts for the LEAP engine to date.
“We are pleased to extend our partnership with Safran, building on the success of Albany’s proprietary 3D weaving technology and our joint efforts on critical components of the LEAP and GE9X engine programnes,” said Bill Higgins, president and CEO of Albany International, which is headquartered in Rochester, New Hampshire. “The goals set for the next-generation of aircraft engines are multi-faceted and technically demanding. Our AEC team is looking forward to further collaboration with our Safran partners to apply advanced composite technologies to the next generation of aircraft engines that meaningfully raise the bar for fuel-efficiency and contribute to a more sustainable future.”
“Based on the successful partnership we have developed with Albany on the LEAP programme, we are looking forward to starting a new chapter of our strategic cooperation,” said Jean-Paul Alary, Safran Aircraft Engines CEO. “Combining Albany’s recognised expertise in weaving with our composites represents a fantastic asset to address our ambitious sustainable goals through next-generation engine programmes.”
Business intelligence for the fibre, textiles and apparel industries: technologies, innovations, markets, investments, trade policy, sourcing, strategy...
Find out more