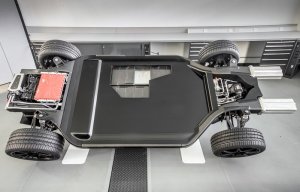
Williams to unveil new approach to EVs
Freudenberg Performance Materials develops new lightweight solutions to seal against electromagnetic radiation.
12th April 2019
Innovation in Textiles
|
Weinheim
Freudenberg Performance Materials develops new lightweight solutions to seal against electromagnetic radiation. © Freudenberg
Electronic components must be protected from disruptions caused by electromagnetic waves. Experts from Freudenberg Performance Materials and Freudenberg Sealing Technologies are working together on ways to provide shielding with plastic housings. In the future, they could partially replace the aluminium versions that have dominated the market until now, the company reports.
Fields of electromagnetic interference often form where electric current flows. When the flow is powerful, in high-performance electric powertrains, for example, the strength of these fields increases, and they can disrupt the signal flow in microprocessors and transmitter-receiver systems. One proven remedy is the encasement of electric components in housings made of a conductive metal. So far, aluminium has been the main tried-and-tested material for this. But its use substantially increases the proportion of aluminium in electric vehicles.
Due to their lack of conductivity, significantly lighter plastics have not been considered as materials so far. But experts from Freudenberg Performance Materials and Freudenberg Sealing Technologies have teamed up to develop processes that can equip plastics with conductive coatings or nonwovens. Early lab tests show excellent values for electromagnetic shielding: up to 99.999999%, according to the manufacturer.
“There are basically two technical approaches to achieving good shielding in the frequency range of 150 kHz to 100 MHz – a spread especially relevant to the drivetrains of electric vehicles,” the company explains. “One of them relies on a specific effect: Electromagnetic waves striking conductive surfaces can be almost entirely deflected. A second approach is to weaken electromagnetic waves at relatively high frequencies in the interior of a material – absorption is the term used to describe this effect. Two processes developed by Freudenberg combine the two effects. The processes offer specific benefits that depend on the size of the component, among other factors.”
Freudenberg Performance Materials has developed a nonwoven that is treated with a special galvanic process. It totally encases individual nonwoven fibres with a copper surface, covered by another material layer to prevent corrosion. Since these nonwovens are produced as endless metered product, the technology is especially suited for components with large surfaces produced in the preforming process.
Housing covers for traction batteries are one example. The trimmed nonwoven can then be inserted and compressed into the tool with the pre-product – which is necessary anyway. An inseparable bond is formed during the setting process. Due to the low density of the nonwoven, an extremely small quantity of the material – a mere 60 grams – is consumed per square meter. That is less than the corresponding weight of normal printer paper. Combined with a lighter-weight plastic carrier material, the result is weight savings of up to one-third compared to aluminium housings. This represents about a 5-kilogram reduction in the weight of a battery housing cover.
For the shielding of fairly small components, Freudenberg Sealing Technologies has developed coatings that deflect electromagnetic waves from their surfaces. The plastic component is coated with an aqueous dispersion whose plastic matrix contains filler offering a high level of electric conductivity. One alternative is to apply the dispersion to a plastic film, which is in turn integrated into the injection moulding tool.
In this process, the highly conductive coating lies inside, so it is well protected from mechanical damage. Long-term tests on material samples show that such coatings display very good aging behavior even at 120°C and completely meet the requirements of the LV 124-2 test standard. The standard sets industry-wide testing processes and boundary values for electrical components permitted for use in cars. The protective coating, the plastic housing and its seal create a unit whose parts are ideally coordinated with one another. Freudenberg Sealing Technologies offers these solutions under the phrase Seal & Shield.
Whatever process is used, neither the coating nor the use of the nonwoven impairs the mechanical properties of the plastic component, the company adds.
In some applications, it is important for the absorption to account for the lion’s share of electromagnetic shielding. This especially applies to the housings for radar sensors that operate in the 77-gigahertz frequency range. If the housing surface were to deflect radar waves, the result could be signal distortion.
Freudenberg Sealing Technologies has developed a composite material that can be processed using injection moulding and, based on early measurements, exhibits much higher absorption rates than commercially available plastics.
Business intelligence for the fibre, textiles and apparel industries: technologies, innovations, markets, investments, trade policy, sourcing, strategy...
Find out more