Hexcel presents composite materials at SAMPE China 2017
Composites
Sustainable rudder for Airbus A320
EcoRudder research project will focus on new generation rudder structure for a single-aisle commercial aircraft.
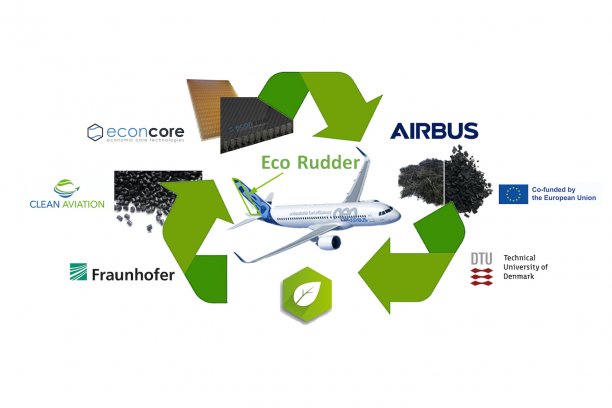
21st April 2023
Innovation in Textiles
|
Leuven, Belgium
Leuven, Belgium headquartered EconCore is working works with Airbus, the Technical University of Denmark (DTU) and Germany’s Fraunhofer research institute on a new green and sustainable type of rudder, based on thermoplastic honeycomb sandwich composites, for the Airbus A320 aircraft.
Airbus, Fraunhofer, DTU and the sandwich core supplier EconCore will develop a new generation green and sustainable rudder structure based on potentially recyclable thermoplastic materials. It forms part of the project FASTER H2, funded by the European Union's Clean Aviation Research Program under Horizon Europe and led by Airbus.
The four partners will collaborate on the work package in FASTER H2, called EcoRudder, which focuses on the development of a new generation rudder structure for a single-aisle commercial aircraft. It is envisaged that the rudder structure will be redesigned and replaced with thermoplastic materials that have the potential to be recycled after the aircraft has been decommissioned.
Within the scope of the project, thermoplastic honeycomb sandwich structures will be produced and evaluated against the requirements for the rudder, and a recycling concept for the panels will be demonstrated. Beside the extensive testing and analysis to ensure that the materials meet all requirements for a certification in a structural aircraft component, also a detailed life-cycle analysis (LCA) will be performed to confirm the reduced CO2 footprint of the new thermoplastic honeycomb sandwich rudder.
Composite sandwich construction has proven to be a very efficient structural concept in structural aircraft parts. In line with today’s sustainability requirements, green composites are expected to replace conventional thermoset materials such as phenolic resin honeycombs and epoxy laminates. This improvement in sustainability has to be achieved without compromising on mechanical requirements such as damage tolerance under extreme environments and unintended loading scenarios. Sufficient robustness and structural integrity against service loads, as well as potentially recycling of the thermoplastic constituent materials, must also be ensured.
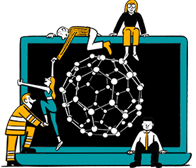
Business intelligence for the fibre, textiles and apparel industries: technologies, innovations, markets, investments, trade policy, sourcing, strategy...
Find out more