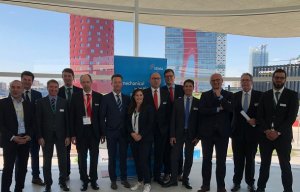
Going digital at ITMA 2019
German industry presents a new edition of the VDMA energy efficiency guide on textile machinery.
13th November 2015
Innovation in Textiles
|
Milan
More than 240 German exhibitors are present in Milan, making Germany one of the largest exhibiting nations at ITMA textile machinery exhibition that started in Italy this week. The sustainable German technology and innovation will be presented to more than 100,000 trade professionals, who are expected to visit the exhibition in the next seven days.
“VDMA and Blue Competence members provide best practice examples for resource and energy saving, sustainable corporate culture and strategies, integration of functions, automation and steps towards Industry 4.0,” said Regina Brueckner, Managing Director Brueckner Trockentechnik and Chairperson of the VDMA Textile Machinery Association.
“Additionally we support our customers with technological advice over the whole manufacturing process as we believe that first class machines also need first class consulting and support.”
Energy efficiency is still a major topic in the textile industry. Therefore the German industry presents a new edition of the VDMA energy efficiency guide on textile machinery. In addition, German experts not only present their innovations but demonstrate the energy savings along the entire textile production chain of well-defined textile product categories.
Calculations cover the full textile production cycle of cotton T-shirts, functional shirts or textile billboards, hygienic nonwovens and woven architectural fabrics.
“These five product examples stand for thousands of textile products. Total energy savings of up to 30% are possible by using German state-of-the-art technology compared to the machinery generation 10 years ago,” explained Karin Schmidt, Head of Technology of VDMA Textile Machinery.
Production of functional T-shirts for sports and leisure clearly show the progress made, the VDMA reports. German technology of 2013 consumes 30% less energy than predecessor machines and components ten years ago.
With their production lines for hydroentangled nonwovens the German mechanical engineering companies did credit to the demand for sustainability. Over a ten years period only, the companies adhering to VDMA have succeeded in saving 27% of energy and in addition big quantities of water and fibre material for the overall production.
For the process of spunlacing/hydroentangling itself, 36 % and for drying of nonwovens 34 % of energy could be saved, according to the VDMA. If the global production of almost one million tons of raw material was run exclusively on German latest world champion technology, it is estimated that an amount of energy of 555 billion watt hours (555 GWh) could be saved every year.
The textile machinery manufacturers affiliated with VDMA are recognized for their leadership with regards to innovations and quality. “They constantly optimize machines, components and technology also in view of sustainability and thus offer the key for energy- and resource-efficient manufacturing processes,” commented Thomas Waldmann, VDMA Managing Director.
The advanced German technology demonstrated at ITMA supports machine operators worldwide, VDMA reports. Intuitive assistant systems, support by databases that hold the sum of the process knowledge, as well as simulation of the entire process cycle, are just some promising developments for optimizing the resource and energy efficiency in textile mills.
Business intelligence for the fibre, textiles and apparel industries: technologies, innovations, markets, investments, trade policy, sourcing, strategy...
Find out more