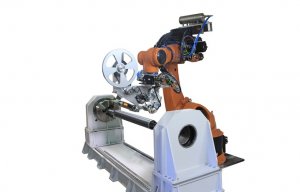
Combined AFP and ATL from Mikrosam
The new cell completes a £36.7 million programme of ten new machines.
6th May 2021
Innovation in Textiles
|
Bristol, United Kingdom
The National Composites Centre (NCC) in Bristol, UK, has installed a new Automated Fibre Placement (AFP) and Automated Tape Layup (ATL) cell.
The cell, created in the UK in partnership with Electroimpact of Flintshire, is uniquely designed to combine both AFP and ATL in a single system, enabling the processes to be used individually or together to create large, complex structures with minimal downtime. The robot is intended for medium to large scale manufacturing with a high performance and accurate motion platform.
The installation completes a £36.7 million programme of ten new and fully digital automated composite manufacturing capabilities that have been installed in the past 18 months.
The AFP process head utilises eight tows, each measuring 12.7mm wide, with either an infrared heater to manufacture thermoset composites, or the novel humm3 flash technology which has been developed by Heraeus Noblelight of Cambridge and tested at the NCC for the manufacture of thermosets at low temperatures (30-60°C) and high temperature thermoplastics or bindered dry fibres (100-300°C).
The ATL head can deposit tapes of 75, 200 or 300mm widths using the same heating systems and material processing capability as the AFP unit.
Vertical and horizontal rotators allow for complex tools to be used to create geometries such as convex and concave panels, large scale diameter pipes, spars or barrel/tower structures. The rotators enable components of up to 4.6 metres diameter, and 7 metres in length to be manufactured. The cell’s flat tables also allow for smaller scale analysis such as material testing or prototype trials to de-risk programmes and build knowledge prior to larger scale projects.
“The NCC’s AFP-ATL capability is a perfect test bed for automated composite manufacturing at a medium to large scale level,” said NCC automation manager Eva Sastres Collardo. “The system will enable new and existing markets to build up their innovation platforms from the ground up, from small scale prototyping and material testing through to full scale demonstrators and data analytics. The output for customers will be the enabling of high-performance products, created at high volume with reduced cost and waste to achieve step change technology.”
“The hybrid cell offers the NCC flexibility to manufacture a range of part geometries using various material types and formats,” added Alastair Gray from Electroimpact. “Furthermore, thanks to the modular nature of the of the end effectors to the motion platform, it is possible for the NCC to future proof its cell to accommodate the very latest in composite head technology and innovation as it becomes available.”
The National Composites Centre is one of seven centres that make up the UK’s High Value Manufacturing Catapult. Opened in 2011, the centre has seen over £200 million investment in capabilities. It has worked with organisations globally to progress the adoption of composite products.
Business intelligence for the fibre, textiles and apparel industries: technologies, innovations, markets, investments, trade policy, sourcing, strategy...
Find out more