Designed to decompose in forests
Technology/Machinery
Flexible staple fibre production made simple
Economical, flexible and compact – this is the motto with which Oerlikon will showcase the Staple FORCE S 1100 at the ITMA Asia this week.
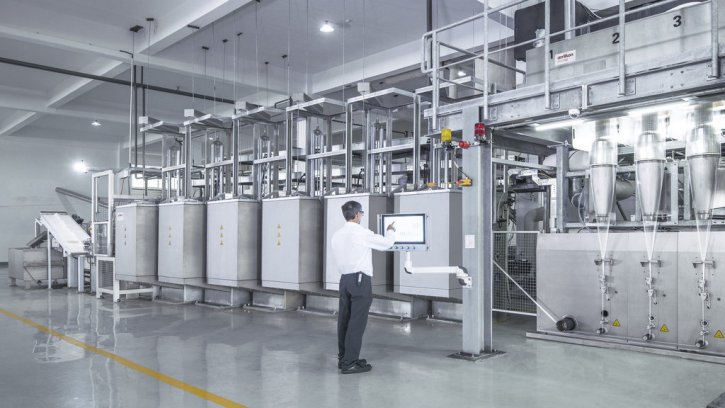
15th October 2018
Innovation in Textiles
|
Shanghai
Economical, flexible and compact – this is the motto with which Oerlikon Neumag will showcase the Staple FORCE S 1100 at the ITMA Asia + CITME 2018, which opened its doors to the international audience in Shanghai earlier today.
“The staple fibre system excels at two things in particular,” the company says. “It produces small batches (up to 15 tons per day) and can be swiftly reconfigured for various requirements, including polymer, dye and titer changes. Its process control system for easy operation is absolutely unique. And all this for a modest initial investment.”
Flexible production
Large-scale staple fibre systems are only conditionally suitable for manufacturing smaller volumes of fibres. This is because frequent stopping and restarting of the system in order to switch raw materials and operating parameters results in expensive downtimes and high wastage. Nevertheless, small batch manufacturing is in demand – for instance, in the case of staple fibre products with changing fashion colours or various titers. And new fibre materials are initially tested and launched in small volumes.
“For this reason, manufacturers already producing staple fibres in large volumes are also interested in additional systems for smaller flexible production,” said Stefan Schäfer, Sales Director Staple Fiber at Oerlikon Neumag.
The Staple FORCE S 1100 has been developed to fulfil these requirements and also offer a special highlight: its innovative process control system. Operators are able to steer the system using just five buttons – stop, back, next, pause and acknowledge, ensuring that operating errors are virtually ruled out. Parameters for the various operating modes are preset to ensure easy start-up. To this end, the operator now only needs to jump from one operating mode to the next using the control unit. And the process parameters for the various fibres manufactured are also stored as a recipe, allowing operators to access them at any time without re-entry. This results in a fibre quality that can be reproduced more accurately, according to the manufacturer.
One-step plant
The Staple FORCE S 1100 is a one-step plant, which spins, draws, crimps, cuts and bales in a single process step. Here, the fibre tow is drawn using godets in a high-speed process. Sets of godets positioned above each other form a stretch duo with its own hood. This is designed to simultaneously provide several benefits: each duo has its own temperature zone under the hood. To this end, the temperatures remain more constant, with no drop-in temperature between the two godets of each duo. Furthermore, the hoods act as steam chests, hence dispensing with the water and steam baths used for steaming the fibre tow in the conventional process. This is also said to reduce energy costs.
“Those investing in the system with its relatively low procurement costs benefit from the simple system commissioning: it is delivered as modular, preinstalled components and a spinning beam with integrated, low-maintenance HTM (Heat Transfer Medium) system. This means that an external boiler with all the corresponding pipes is no longer necessary, dispensing with expensive, time-consuming welding,” the company continues.
The installed Staple FORCE S 1100 is 30 metres long, 12 metres wide and manufactures up to 15 tons of staple fibres of extremely even quality a day.
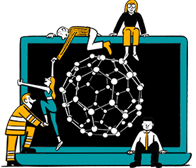
Business intelligence for the fibre, textiles and apparel industries: technologies, innovations, markets, investments, trade policy, sourcing, strategy...
Find out more